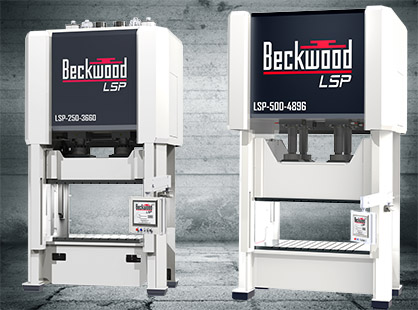
The aerospace industry demands incredibly high precision, force, and reliability from forming equipment like presses. Traditionally, hydraulic presses have been there to deliver the intensive performance that the aerospace industry needs; however, as time goes on, the challenges of hydraulics in these applications have become increasingly clear.
An area that has demonstrated a high need for more suitable press equipment is hot forming, a process which utilizes heated platens on a hydraulic press to more easily form high-strength materials at lower tonnages. This process is crucial to producing aerospace components which feature complex geometries. Hot forming greatly reduces the risk of defects that are more common in cold forming like cracking, spring-back, and residual stress.
In superplastic forming (SPF), a type of process adjacent to hot forming, high-strength alloy materials are formed with tools that are heated up to 2,000°F. These heated platens typically sit below the hydraulic cylinders. While this technology is incredibly useful for shaping high strength materials, it also comes with its own set of unique safety considerations regarding the use of high heat and hydraulic fluid. For this reason, it is common for SPF hydraulic presses to require more frequent pauses in production for scheduled preventative maintenance and leak checks.
As a leader in designing and building presses for the aerospace industry, we understand the complexity of the challenges faced by our customers better than any other manufacturer in the US. Our 40 years of industry experience put us in a unique position to tackle these pressing issues.
At FABTECH 2022, Beckwood revealed a game-changer for the press industry: the LSP, short for linear servo press. This piece of equipment built and improved upon the foundational strengths of traditional presses and eliminated the risks and maintenance needs that come with the use of hydraulic fluid. These upgrades make linear servo technology a great option for use in forming high quality aerospace components.
Linear Servo Driven Presses Provide Unparalleled Process Controls
A linear servo press gives operators far more control over process parameters compared to a traditional hydraulic press. Each aspect of the machine stroke is fully programmable- including speed, ram position, and force- to offer maximum precision and forming flexibility.
Full tonnage can be delivered at any point of the machine stroke, and our standard linear servo presses are all equipped with dwell capabilities. This is especially useful for compression molding applications like those commonly used in aerospace part forming.
Active leveling controls work to the benefit of hot forming in that the linear actuators are servo driven and electronically synchronized, thereby providing active leveling throughout the stroke of the press. This ensures bed to ram parallelism; and depending on the actuator configuration, it can provide left to right parallelism control or even the addition of front to rear control.
From hot forming to super plastic forming, linear servo technology can tackle your aerospace forming needs. Contact us today to learn more and get in touch with our Solutions Team.
Contact Beckwood Press
Servo Presses Eliminate Hydraulic Fluids and Their Limitations
As previously discussed, hydraulic fluids are something of a double-edged sword in hydraulic press applications. While the pressurized fluid is what provides traditional hydraulic presses their capabilities, it also serves as a major drawback in hot forming and SPF applications.
Astoundingly, the design of our high-tonnage linear servo presses completely eliminates the need for pressurized hydraulic fluid and delivers even more remarkable performance.
By eliminating the use of hydraulic fluid, all of the risks and hazards associated with it are eliminated as well. This makes servo presses a safer option than hydraulic presses in more ways than one. From a workplace standpoint, servo presses remove the risk of fluid spills on the shop floor. From a process standpoint, the absence of hydraulic fluid helps mitigate the risk of part contamination as the pressing takes place. In aerospace applications where part quality is paramount, the repeatability and precision offered by linear servo technology minimizes opportunities for errors and discrepancies between production runs.
On top of improving safety overall for machine operators and site personnel, subtracting hydraulic fluid drastically improves the efficiency of hot forming and SPF operations for shaping high-strength steel and titanium alloys. Downtime is further reduced by the simplicity of the lean design principles that went into engineering the LSP. Compared to a traditional hydraulic press, linear servo systems employ up to 80% less individual machine components. This makes routine maintenance much more infrequent; users can get millions more cycles between scheduled press maintenance when using the technology.
The marvel of linear servo technology is something you have to see to believe. Click here to watch a video showcasing our high-tonnage LSP in action.
To learn even more about Beckwood’s experience serving the aerospace industry, be sure to read up on our industry publications. You can even read and download our free comprehensive guide to all things Beckwood in aerospace right here. Our Solutions Team would be happy to answer any questions you might have regarding engineering solutions for aerospace presses, including hydraulic press retrofitting. Contact us today, and soon enough your business can become our next success story.