Hydraulic Press Machinery for Aerospace Manufacturing
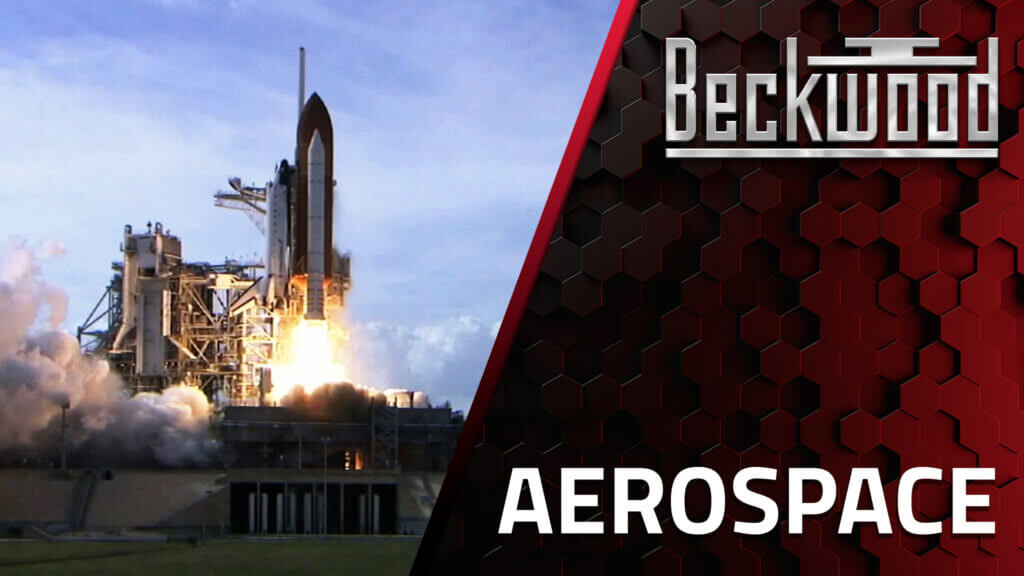
Aerospace Machining vs. Pressing
Create Near-Net Aerospace Components with TRIFORM
Sheet HydroForming Presses
Going beyond traditional press equipment, Beckwood has the expertise in specialized aerospace manufacturing equipment thanks to the ingenuity of our TRIFORM Engineers. Beckwood’s Triform™ sheet hydroforming presses thrive in low-volume, high-mix production environments where tool changes occur frequently and manufacturing processes are continually refined. Sheet hydroforming presses use a pressurized rubber diaphragm and a single un-mated tool to create near-net-shape parts in just one cycle. Triform’s proprietary In-Sight tool even allows you to view forming progress at any point throughout a cycle and adjust the recipe to achieve optimum forming results. This feature greatly expedites R&D and reduces costs and scrap.
Learn More >Triform Draw Sheet Hydroforming
Going beyond traditional press equipment, Beckwood has the expertise in specialized aerospace manufacturing equipment thanks to the ingenuity of our TRIFORM Engineers. Beckwood’s Triform™ sheet hydroforming presses thrive in low-volume, high-mix production environments where tool changes occur frequently and manufacturing processes are continually refined. Sheet hydroforming presses use a pressurized rubber diaphragm and a single un-mated tool to create near-net-shape parts in just one cycle. Triform’s proprietary In-Sight tool even allows you to view forming progress at any point throughout a cycle and adjust the recipe to achieve optimum forming results. This feature greatly expedites R&D and reduces costs and scrap.
Learn More >Triform Ring Expanders
Going beyond traditional press equipment, Beckwood has the expertise in specialized aerospace manufacturing equipment thanks to the ingenuity of our TRIFORM Engineers. Beckwood’s Triform™ sheet hydroforming presses thrive in low-volume, high-mix production environments where tool changes occur frequently and manufacturing processes are continually refined. Sheet hydroforming presses use a pressurized rubber diaphragm and a single un-mated tool to create near-net-shape parts in just one cycle. Triform’s proprietary In-Sight tool even allows you to view forming progress at any point throughout a cycle and adjust the recipe to achieve optimum forming results. This feature greatly expedites R&D and reduces costs and scrap.
Learn More >Triform Stretch Forming
Going beyond traditional press equipment, Beckwood has the expertise in specialized aerospace manufacturing equipment thanks to the ingenuity of our TRIFORM Engineers. Beckwood’s Triform™ sheet hydroforming presses thrive in low-volume, high-mix production environments where tool changes occur frequently and manufacturing processes are continually refined. Sheet hydroforming presses use a pressurized rubber diaphragm and a single un-mated tool to create near-net-shape parts in just one cycle. Triform’s proprietary In-Sight tool even allows you to view forming progress at any point throughout a cycle and adjust the recipe to achieve optimum forming results. This feature greatly expedites R&D and reduces costs and scrap.
Learn More >Hot Forming & Superplastic Forming Presses
Compression Molding Presses
Compression molding presses utilized heated or cooled platens to achieve a desired forming temperature. They are extremely versatile tools which can be used to shape a wide range of materials from lightweight composites to high-strength alloys. This makes them excellent for aerospace manufacturing facilities which often produce a low volume of high-variety parts. We can manufacture custom compression molding presses for:
• Thermoforming
• Injection Molding
• Composite Forming
• Extrusion Forming
• Reaction Injection Molding
• Powder Compacting
• HDPE Sheet Making
• UHMW Sheet Making
Custom Hydraulic Presses for Space Equipment
Linear Servo Press Technology
Aerospace manufacturing processes, like complex draw work and stamping high-strength alloys, require tight process control. With Beckwood LSP™, you can easily program ram position, travel distance, and speeds for maximum productivity. With instant feedback for diagnostics and data acquisition to record and measure torque, force, position, and time, no press offers greater precision or better part quality. With presses ranging from 125 – 500 tons, Beckwood LSP™
offers the highest tonnage capacity of any linear servo press available. High precision, uptime, reliability, and unmatched forming flexibility are pillars of this world-class press technology. The use of a servo motor and linear motion system allows for greater control over the pressing process, including the ability to adjust the press force, speed, and stroke. This makes linear servo presses ideal for stamping of high-strength sheet metals, complex draw forming, progressive die forming, assembly, and any application that requires high-precision and/or accuracy.
For low-tonnage part forming and assembly operations, our line of EVOx servo-electric presses has the right press for the job. With options for actuator size, frame type, dwell time, heated platens, safety features, and more, these machines can be configured to suit your aerospace manufacturing needs. The EVOx is available in a tonnage as low as 2.5 tons, up to as high as 50 tons. Positional repeatability to within ±0.0005″ is made easy with this machine designed for high accuracy and high precision.