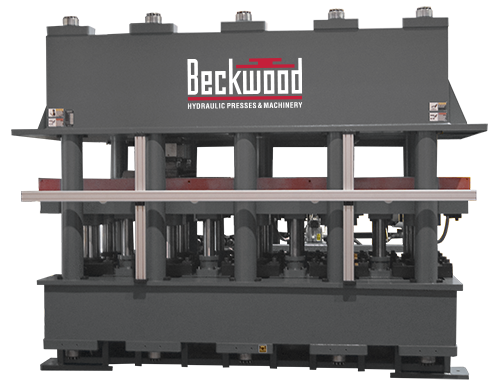
A multi post press provides extreme flexibility throughout the forming process, especially during off-center loading applications. Adding extra posts to a press can greatly reduce the span of the machine, resulting in lower steel costs and a reduced loading height.
Multi Post Press Success Story
An aerospace honeycomb panel manufacturer approached Beckwood with a unique manufacturing challenge that could not be solved with a ‘standard’ press solution. They needed a 1,000-ton heated platen press that could be off-center loaded, run both large (44” x 140”) and small parts, and provide an ergonomically-friendly load height without any special foundations. Beckwood responded with a fully custom 10-post press, otherwise known as a multiple post press, that features five individual zones of force control.
Because the customer was loading parts exclusively through the narrow openings of the press, wide side access was not necessary. This allowed Beckwood to engineer a press with 10 posts, drastically reducing the span which resulted in lower steel costs and the opportunity to reduce the loading height of the machine to an optimum level.
The five zones of force control over the distance of the ram platen allows the press to run both small and large parts with ease. When large parts are being run, all of the zones are synchronized to allow consistent force across the surface of the part. When smaller parts are being processed, individual zones that are unused can be ‘turned off’ to ensure the press maintains parallelism during off center loading.
High temperature rollers were installed in the lower platen to assist with the manual loading, unloading, and indexing of parts across the 140” long platen area. The result of the customization is a versatile machine that could not be matched by any ‘cataloged’ press offering.