Triform installed a new deep draw sheet hydroforming press for an automotive parts manufacturer specializing in rapid prototyping. The 25-10-12DD model features a 25” diameter forming area, 10,000 PSI of forming pressure and a 12” draw depth capacity. This is the second deep draw Triform for this company’s operation, with their having previously installed a model 16-10-7DD. Read More
Archives: News Items
News Items will appear in the News section.
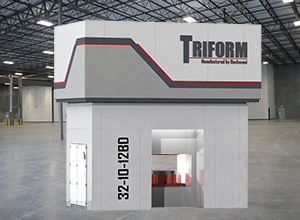
Triform 32” Deep Draw Sheet Hydroforming Press Installed in Leading Aerospace OEM Facility
The Triform 32-10-12DD, features a 32” diameter forming area, 10,000 PSI of forming pressure and a 12” depth-of-draw. The 32-10-12DD allows forms complex geometries by precisely controlling both the bladder pressure and the punch position. Read More
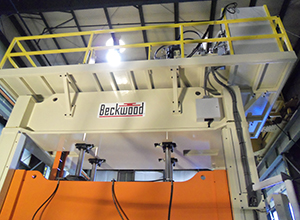
Beckwood to Build Custom Trimming Press for Automotive Industry Supplier
Beckwood Press Company has been chosen to engineer and build a custom 165-ton, gib-guided trimming press with quick die change system for a leading manufacturer of interior and exterior automotive components, including plastic molded, painted and assembled parts. Read More
Beckwood Installs Custom Heated Compression Molding Press for Aerospace Cabin Interiors
Beckwood recently installed an 800-ton custom hydraulic heated platen press which will be used in a compression molding application to thermoform aerospace cabin interiors. The 60" x 108" bed and ram platens are heated via a hot oil system for ultimate temperature uniformity. Read More
Beckwood Manufactures Gib-Guided Coining Press
Beckwood eningeered a 230-ton hydraulic gib-guided press used to manufacture tooling for the medical industry. Features of the made-to-order coining press include a custom bed cushion and part ejection system for integration with the customer’s existing tooling. Read More
Beckwood Delivers Multi-Ram Press for Hot Forming/Water Quenching Application
Beckwood recently delivered a 150 Ton, 5-Post, dual-ram hydraulic press to a leading manufacturer of agricultural disks. The press, engineered to maintain pressure on the part during both the hot forming process and subsequent in-die water quench, has eliminated three steps from the customer's production cycle. Read More
10-Post Hydraulic Press
Beckwood recently delivered 10-post hydraulic heated platen press with 5 zones of force control for use in a compression molding application to manufacture honeycomb panels. The 10-post design significantly reduced the structural span of the press, allowing the overall height to be minimized while maintaining 'infinite life' structural classification. Read More
Aerospace Supplier Expands Capacity
In 2011, aircraft interior systems manufacturer Aerosud Holdings Pty., approached Beckwood Press to solve a bottleneck in the production of aluminum canisters for the Airbus A320. The canisters were previously drawn to 6.5” deep through a grueling 6-step annealing process, which often resulted in high scrap rates due to excessive thinning. Beckwood worked with Aerosud to transfer the production of these aluminum canisters to a TRIFORM 16-10-7DD to great success. Material thinning was reduced to just 10%, production costs were reduced by 25%, and scrap rates are now below 1%. In addition, the canisters now have a cleaner, more uniform appearance and are better suited for the welding process in the final assembly. As a result of the incredible success... Read more » Read More
Beckwood Delivers 9th Press to Aerospace OEM Giant
Beckwood Delivers 9th Press in Ongoing Partnership with Large Aerospace OEM Here at Beckwood we’re ecstatic to share that we are gearing up to deliver our 9th press machine to one of the largest aerospace manufacturers in the world over a period of just 3 years. What started as a standalone order for a single division at the OEM has quickly evolved into an ongoing partnership that spans across multiple divisions. This partnership began in 2022 when one of the OEM’s larger manufacturing divisions ordered 6 hydraulic trimming presses to use in finishing operations for their die-cast parts. These initial hydraulic press machines helped breathe new life into the division’s manufacturing processes by increasing part quality and throughput. Word rapidly... Read more » Read More
A&D Job Shop Expands Deep Draw Capabilities and Modernizes Operations
A&D Job Shop Expands Deep Draw Capabilities and Modernizes Operations Building on a relationship of over 9 years, Beckwood is assisting Globe Engineering to expand their hydroforming operations with their very first TRIFORM deep draw machine. This delivery was planned in collaboration with Kansas Oklahoma Machine Tools (KOMT), one of the Midwest’s leading machinery distributors. Globe Engineering is no stranger to hydroforming as they purchased their first Cincinnati deep draw hydroform in 1964. Their new TRIFORM machine signifies the beginning of Globe Engineering’s efforts to modernize their hydroforming operation after building the foundation of a legacy in this manufacturing niche. “We are very excited to partner with Globe Engineering to support the modernization of their hydroform operation, while also... Read more » Read More