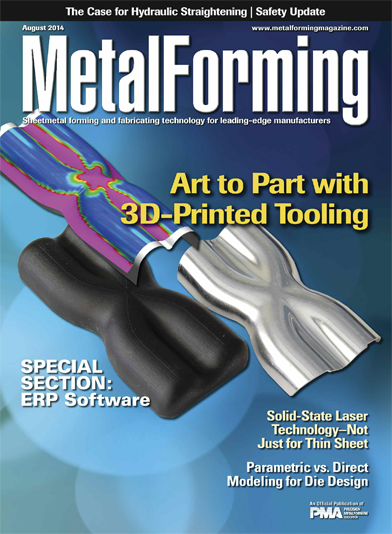
St. Louis, MO – Beckwood Press Company, a leading manufacturer of custom hydraulic and servo-electric presses, automation systems, and the Triform line of sheet hydroforming presses, has announced the commencement of a new educational circuit to inform individuals in the metal forming industry about new developments in rapid prototyping. The effort will focus specifically on the use of simulation software, 3D printed tooling, and Triform sheet hydroforming which can be used in conjunction to develop quality parts faster.
This educational circuit includes a webinar hosted by Beckwood and MetalForming Magazine (MFM), a one-hour session at FABTECH in Atlanta, online self-guided presentations, and one-on-one consultations on the subject of new technologies for rapid prototyping in low-volume part production. To launch this educational tour, MetalForming Magazine published an article in the August issue entitled “Art to Part with 3D Printed Tooling.” The article highlights the use of simulation software, 3D printed tooling, and Triform sheet hydroforming presses to illustrate the advantages each can bring to an operation.
The first MFM webinar will occur on October 2, 2014, and FABTECH session entitled “How to Go from Concept to Finished Part in Less than 24 Hours,” will be held on November 13, 2014. Beckwood will provide additional details to parties as they are released.
“There is a new industrial revolution taking place. Manufacturers are using simulation software, 3D printed tooling, and sheet hydroforming presses to go from a concept to a finished part within hours,” said Beckwood President, Jeffrey Debus. “This trifecta of technology is changing the way part manufacturers go to market and destroying old beliefs about cost, capability, and development time. We know every metal forming company can benefit from the efficiencies these technologies bring, and we want every company to be aware of the options available to them.”